Stress-Strain Curve Analysis Using MATLAB
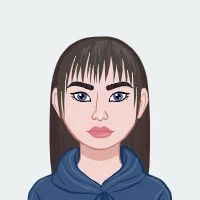
In materials science, stress-strain curves are fundamental tools for evaluating how materials behave under different forces. Stress, measured in units of force per unit area (such as Pascals or megapascals), represents the internal resistance of a material to deformation. Strain, on the other hand, quantifies the extent of deformation relative to the material's original dimensions.
Stress-strain curves typically exhibit distinct phases: elastic, plastic, and sometimes failure. The elastic region shows linear deformation in response to applied stress, governed by Hooke's Law. Beyond this point, materials enter the plastic region where permanent deformation occurs. The ultimate stress marks the maximum stress a material can withstand before failure, while the rupture point indicates complete structural failure.
Understanding these curves helps engineers and scientists predict material behavior under various conditions, which is crucial for designing structures that can withstand expected stresses without failure. MATLAB facilitates this understanding by allowing precise visualization and analysis of stress-strain data, enabling users to extract critical parameters such as yield strength, ultimate strength, and modulus of elasticity with accuracy and efficiency. Make sure to complete your MATLAB homework to proficiently utilize these tools for materials analysis and engineering design.
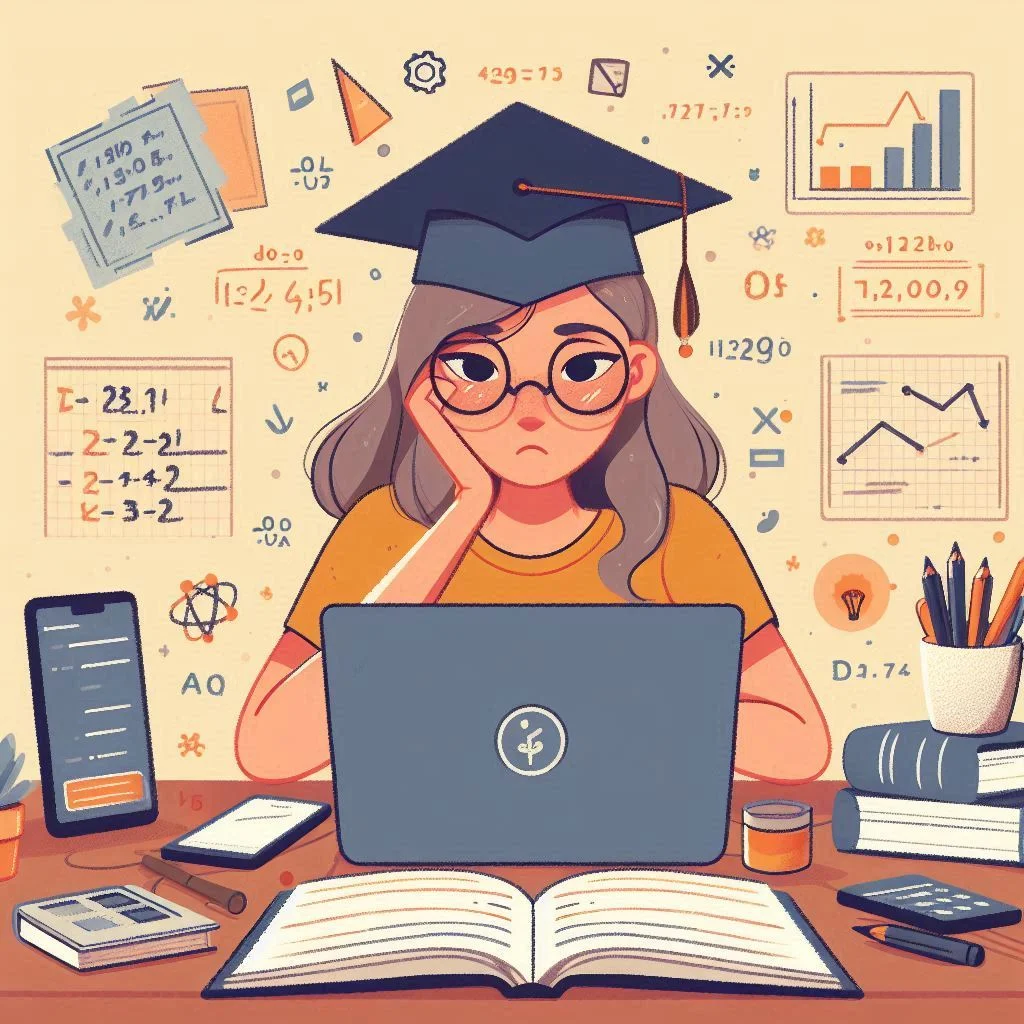
MATLAB Basics for Stress-Strain Analysis
Before delving into stress-strain curve analysis, mastering essential MATLAB functions is essential. MATLAB's versatility in handling large datasets, generating high-quality graphs, and performing complex calculations makes it an invaluable tool for engineers and researchers alike.
To begin, familiarity with MATLAB's scripting environment and basic syntax is essential. Functions such as plot, xlabel, ylabel, and title are fundamental for creating clear and informative stress-strain plots. MATLAB also offers powerful data manipulation capabilities, enabling users to import, clean, and preprocess experimental data efficiently.
Moreover, MATLAB's graphical user interface (GUI) tools like plottools simplify the customization of plots, allowing users to add error bars, annotations, and legends to enhance data visualization. This level of flexibility is crucial for accurately depicting experimental results and conveying findings effectively in academic and professional contexts.
By mastering these foundational MATLAB skills, students and researchers can leverage the software's computational power to analyze complex stress-strain data sets comprehensively. This proficiency not only enhances their understanding of material behavior but also equips them with essential skills for future research and engineering endeavors.
Plotting Stress-Strain Curves
The process of plotting stress-strain curves in MATLAB involves several key steps to ensure accurate representation and analysis of experimental data. MATLAB's robust plotting capabilities allow users to visualize both grips and extensometer data on a single plot, providing a clear comparison of material behavior under different testing conditions.
Begin by importing experimental data into MATLAB, ensuring data integrity and consistency. Utilize MATLAB's plot function to generate initial stress-strain curves, incorporating features such as color-coded lines for different materials or experimental conditions. Adding a 0.2% offset line is crucial for determining the yield strength, a critical parameter in material characterization.
To enhance data clarity and interpretation, MATLAB enables the incorporation of error bars, indicating uncertainties in measured data points. This feature is essential for conveying the reliability of experimental results and facilitating informed decision-making in materials research and engineering applications.
Furthermore, MATLAB supports the plotting of true stress-strain curves, which account for changes in cross-sectional area during deformation. This advanced capability provides a more accurate representation of material behavior under extreme conditions, enhancing predictive modeling and design optimization efforts.
By following these structured steps in MATLAB, students and researchers can effectively analyze and visualize stress-strain data, gaining deeper insights into material properties and performance. This proficiency not only strengthens their technical skills but also prepares them for tackling real-world engineering challenges with confidence
Data Analysis and Interpretation
Data analysis in stress-strain curve experiments involves organizing and interpreting experimental results to derive meaningful conclusions about material properties. MATLAB offers powerful tools for handling and analyzing large datasets, ensuring accuracy and reliability in scientific investigations.
Once stress-strain curves are plotted, MATLAB facilitates the creation of organized tables that compile all experimental measurements alongside their uncertainties. This organized approach allows researchers to systematically compare and analyze data across different materials or experimental conditions.
In addition to lab measurements, MATLAB enables users to incorporate published densities of materials into their analyses. This comparative approach provides valuable insights into material characteristics and supports the validation of experimental findings against established benchmarks.
Further analysis involves calculating and visualizing key parameters such as ultimate stress and strain, rupture stress and strain, and true rupture stress and strain. MATLAB's computational capabilities simplify these calculations, ensuring consistency and accuracy in results interpretation.
Moreover, MATLAB facilitates the determination of yield stress and strain using grips and extensometer data, essential for assessing material strength and performance under specific loading conditions. The inclusion of uncertainties in these calculations enhances the robustness of experimental conclusions and supports informed decision-making in engineering and scientific applications.
Advanced Analyses: Modulus and Toughness
Advanced analysis using MATLAB extends to calculating modulus of toughness and resilience, as well as Young's modulus for grips and extensometer data. These parameters provide critical insights into a material's ability to absorb energy before failure and its stiffness under applied loads, respectively.
Modulus of toughness quantifies the amount of energy a material can absorb per unit volume before fracture, essential for evaluating its suitability in structural applications. MATLAB's numerical integration tools facilitate the accurate calculation of this parameter from stress-strain data, aiding in material selection and design optimization.
Similarly, Young's modulus, or modulus of elasticity, measures a material's stiffness and its ability to resist deformation under tensile or compressive loads. MATLAB's capabilities in curve fitting and regression analysis enable precise determination of Young's modulus from experimental stress-strain curves, supporting rigorous materials characterization and performance prediction.
Additionally, MATLAB assists in calculating percent area reduction and percent elongation, crucial metrics for assessing material ductility and deformation characteristics. These analyses contribute to a comprehensive understanding of material behavior under different loading conditions, guiding engineering decisions and optimizing performance in diverse applications.
Comparative Analysis of Materials
Comparative analysis using MATLAB facilitates side-by-side comparisons of stress-strain curves and material properties, aiding researchers in identifying trends and anomalies across different materials or experimental scenarios. MATLAB's plotting capabilities allow users to overlay stress-strain curves of multiple materials, facilitating visual comparison and analysis.
Error bars incorporated into MATLAB plots provide insights into the variability and uncertainty associated with experimental data, enhancing the reliability of comparative analyses. By quantifying differences in ultimate stress and strain, rupture stress and strain, yield stress and strain, Young's modulus, and Poisson ratio among materials, MATLAB supports informed decision-making in materials selection and design.
Moreover, MATLAB enables researchers to evaluate percent differences from published values for critical material properties, such as ultimate stress and strain. This validation process ensures the accuracy and reliability of experimental findings, bolstering confidence in materials characterization and performance assessment.
By leveraging MATLAB's robust analytical tools, researchers can conduct rigorous comparative analyses that contribute to advancements in materials science and engineering. This systematic approach enhances understanding of material behavior under varying conditions, facilitating innovation and optimization in diverse industrial and academic settings.
Conclusion
In conclusion, MATLAB emerges as an indispensable tool for analyzing stress-strain curves and deriving critical insights into material properties and performance. By guiding users through the process of plotting, analyzing, and interpreting stress-strain data, MATLAB enhances accuracy, efficiency, and reliability in materials research and engineering applications.
The comprehensive capabilities of MATLAB in handling large datasets, performing complex calculations, and visualizing experimental results empower researchers to make informed decisions and drive advancements in materials science. Whether investigating mechanical properties, assessing material durability, or optimizing design parameters, MATLAB facilitates rigorous analysis and fosters innovation in diverse fields.